|
ACCESS THE FULL ARTICLE
No SPIE Account? Create one
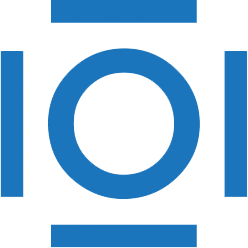
CITATIONS
Cited by 2 scholarly publications and 3 patents.
Semiconducting wafers
Etching
Diffractive optical elements
Coating
Optical lithography
Thin film coatings
Bottom antireflective coatings