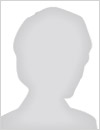
The Vera C. Rubin Observatory is poised to achieve its highly anticipated first light in early 2025, marking the start of an era of transformative observational capabilities. As the observatory nears its first light, the commissioning of the Active Optics System (AOS) becomes increasingly critical. Comprising an open-loop and a closed-loop component, the AOS delivers real-time corrections for the alignment and mirror surface perturbations, ensuring seeing-limited image quality across the 3.5-degree field of view.
In this paper, we present a thorough examination of recent advancements in the AOS at the Rubin Observatory. We begin by detailing the enhancements in the open-loop system, focusing on the improvement of Look-Up Tables (LUTs) for the mirror bending modes and the alignment of optical elements. Next, we discuss the closed-loop control improvements, particularly our novel approach using double Zernike polynomials. This method addresses camera rotation by defining the sensitivity matrix and the reference wavefront with a double Zernike expansion, thereby improving the system’s adaptability to varying observational conditions. Finally, we address improvements made to eliminate degeneracies within the system’s degrees of freedom, and discuss the upcoming verification phases during on-sky testing with the Commissioning Camera (ComCam).
Overall, these initial open-loop verifications and closed-loop algorithmic improvements not only mark significant progress towards full-system verification with LSST Camera, but also refine the capabilities of the AOS, which is key for maintaining long-term operational efficiency and achieving the required image quality.
By creating clear and easily understandable visual technical documentation, LSST minimizes both, technical and personnel risks by ensuring workers fully understand all aspects of the required task. By illustrating what tools to use and where to use them, LSST protects the health and safety of their workers and equipment, while streamlining the construction process. These documents also facilitate educating new employees on best practices.
During observing, or Active Mode2, the M1M3 mirror is supported by an array of 156 support and figure control actuators consisting of 268 pneumatic cylinders that react to gravity and inertial loads and provide figure error correction. Load cells on the actuators measure forces that are communicated to the M1M3 control system. However, the figure actuators do not define the mirror position. This is defined with six axially stiff linear actuators called hardpoints3 arranged in a hexapod pattern to restrain rigid body motion of the mirror in a kinematic fashion. By adjusting the length of each hardpoint, the mirror can be adjusted in all six degrees of freedom with respect to the cell. Displacement sensors and load cells on the hardpoints communicate displacements and forces to the control system, which processes the telemetry and issues force corrections to the figure actuators to zero out any loads and moments on the hardpoints.
In Static Mode, the M1M3 mirror is no longer supported by figure actuators and the position sensing of the hard point hexapod is inactive. A second support system consisting of 288 wire rope isolators called Static Supports come into play. The static supports mechanically capture the mirror whether in Active or Static Mode and in the event the mirror experiences motion beyond the active motion range in any direction. The static supports also safely support the mirror during seismic events for all elevation angles. In active mode, the static supports do not contact the mirror and thus, do not affect the mirror positioning or figure.
This paper focuses on the detailed design, development, testing, integration, and current status of the M1M3 pneumatic figure actuators.
View contact details